编辑:穿孔机厂家,来源:维基百科,浏览量:24,时间:2022-08-19 19:45
一种电火花机床用工装夹具,电火花机床的结构,电火花线切割加工常用的夹具主要有
关于一种电火花机床用工装夹具内容导航:
1、一种电火花机床用工装夹具
高速走丝的线切割机床的电极丝(钼丝)运动速度快通常为8~12米/秒,而且是双向往返循环运行,在加工过程中很容易发生断丝。如果在切割工件过程中多次断丝,不仅会造成一定的经济损失,而且会带来重新绕丝的麻烦;不仅耽误时间,而且会在工件上产生断丝痕迹,影响加工质量,严重的会造成工件报废。下面探讨下高速走丝线切割机床在工作中经常出现的断丝原因及解决办法:
1 钼丝
钼丝的松紧程度。如果钼丝安装太松,则钼丝抖动厉害,不仅会造成断丝,而且由于钼丝的抖动直接影响工件表面粗糙度。但钼丝也不能安装得太紧,太紧内应力增大,也会造成断丝,因此钼丝在切割过程中,其松紧程度要适当,新安装的钼丝,要先紧丝再加工,紧丝时用力不要太大。钼丝在加工一段时间后,由于自身的拉伸而变松。当伸长量较大时,会加剧钼丝振动或出现钼丝在贮丝筒上重叠。使走丝不稳而引起断丝。应经常检查钼丝的松紧程度,如果存在松弛现象,要及时拉紧。
钼丝安装。钼丝要按规定的走向绕在贮丝筒上,同时固定两端。绕丝时,一般贮丝筒两端各留10mm,中间绕满不重叠,宽度不少于贮丝筒长度的一半,以免电机换向频繁而使机件加速损坏,也防止钼丝频繁参与切割而断丝。
机床上钼丝引出处有挡丝棒,挡丝棒是由两根红宝石制成的导向立柱,挡丝棒不像导轮那样作滚动运动,他们直接与钼丝接触,作滑动摩擦。因此磨损很快,使用不久柱体与钼丝接触的地方就会形成深沟,必须及时检查并进行翻转和更换,否则会出现叠丝断丝。
2 运丝机构
线切割机的运丝机构主要是由贮丝筒、线架和导轮组成。当运丝机构的精度下降时(主要是传动轴承),会引起贮丝筒的径向跳动和轴向窜动。贮丝筒的径向跳动会使电极丝的张力减小,造成丝松,严重时会使钼丝从导轮槽中脱出拉断。贮丝筒的轴向窜动会使排丝不匀,产生叠丝现象。贮丝筒的轴和轴承等零件常因磨损而产生间隙,也容易引起丝抖动而断丝,因此必须及时更换磨损的轴和轴承等零件。贮丝筒换向时,如没有切断高频电源,会导致钼丝在短时间内温度过高而烧断钼丝,因此必须检查贮丝筒后端的行程开关是否失灵。要保持贮丝筒、导轮转动灵活,否则在往返运动时会引起运丝系统振动而断丝。绕丝后空载走丝检验钼丝是否抖动,若发生抖动要分析原因。贮丝筒后端的限位挡块必须调整好,避免贮丝筒冲出限位行程而断丝。挡丝装置中挡块与快速运动的钼丝接触、摩擦,易产生沟槽并造成夹丝拉断,因此也需及时更换。导轮轴承的磨损将直接影响导丝精度,此外,当导轮的V型槽、宝石限位块、导电块磨损后产生的沟槽,也会使电极丝的摩擦力过大,易将钼丝拉断。这种现象一般发生在机床使用时间较长、加工工件较厚、运丝机构不易清理的情况下。因此在机床使用中应定期检查运丝机构的精度,及时更换易磨损件。
1 断丝原因的分析及解决办法
1.1 与电极丝相关的断丝
(1)丝张力及走丝速度。对于高速走丝线切割加工,广泛采用?0.06~0.25mm的钼丝,因它耐损耗、抗拉强度高、丝质不易变脆且较少断丝。提高电极丝的张力可减少丝振的影响,从而提高精度和切割速度。丝张力的波动对加工稳定性影响很大。产生波动的原因是:贮丝筒上的电极丝正*时张力不一样;工作一段时间后电极丝又会伸长,致使张力下降(一般认为张力在12~15N较合适人 张力下降的后果是丝振加剧,极易断丝。
随着走丝速度的提高,在一定范围内,加工速度也会提高。同时走丝速度的提高有利于电极丝把工作液带人较大厚度的工件放电间隙中,有利于电蚀产物的排除和放电加工的稳定。但欲速则不达,走丝速度过高,电极丝抖动严重,反而破坏了加工的稳定性,这不仅使加工速度下降,而且加工精度和表面粗糙度都会变差,并易造成断丝。但走丝速度也不能过低,否则加工时由于损耗大,也易断丝,一般经验以小于10m/s为宜。
(2)电极丝的选择。电极丝的选择不外乎是电极丝的种类及直径。通常电火花线切割加工所用的电极丝材料应具有良好的导电性,电子溢出功应小,抗拉强度大,耐电腐蚀性能好.丝本身不得有弯折和打结现象。其材料通常有钼丝、钨丝、钨钼丝、黄铜丝、铜钨丝等。其中以钼丝和黄铜丝用得最多。采用钨丝加工,可获得较高的加工速度,但放电后丝变脆,易断丝,应用较少。故一般在走丝速度较慢、弱电规准时使用。钼丝熔点、抗拉强度低,但韧性好,在频繁的急冷急热的变化中,丝质不易变脆而断丝,因此,尽管有些性能不如钨丝好,但仍是目前使用最为广泛的一种电极丝。钨钼丝(钨、钼各50%加工效果比前两种都好 故使用寿命和加工速度都比钼丝高,但价格昂贵。铜丝的加工速度高,加工过程稳定,但抗拉强度差,损耗也大,一般在低速走丝线切割加工中使用较多。综上所述,电极丝的种类应根据加工情况而定。否则会常常引起断丝。
对于高速走丝线切割加工,一般电极丝直径在?0.06~0.25mm之间,常用的在?0.12~0.18mm之间。需获得精细的形状和很小的圆角半径时,则选择?0.04mm的电极丝。电极丝选择得当,会大大减少断丝的发生。
(3)新钼丝及钼丝自断。新钼丝表面有一层黑色氧化物,加工时切割速度快,工件表面呈粗黑色,这时电源能量太大,易断丝。因此对于新钼丝,加工电流需适当减小,等电极丝基本发白后,即可恢复正常电参数。
当机床较长时间未用,待使用时,发现钼丝已断。这是温差使材料热胀冷缩,加上钼丝本身的张力作用而绷断。若机床停用,应将贮丝筒摇至末端并松掉钼丝。
1.2 与工件相关的断丝
(1)加工薄工件时的断丝。薄工件一般指其厚度在3mm以下。其断丝的主要原因是:线架上下导丝轮的开距是固定的,一般约70mm左右。当切割薄工件时,在高速走丝的情况下,电极丝失去了加工厚工件时产生的冷却液的阻尼作用,加上火花放电的影响银丝易抖动。解决的办法是,可调整加工电压至 50V左右;调整加工电流在 0.3A左右,调整脉宽,使之小于10?m;减小钢丝抖动,如贮丝筒是直流电机拖动的,可改变电枢电压,降低转速;如是交流电机拖动的,则在三相的任意二相中串接一只10~15?、7 5W的线绕电阻,降低相电压,使其换向过渡时间稍长,实现软换向,可有效减少抖动;在上下导轮之间采用辅料加厚的方法,加大厚度,增加阻尼,也可防止钼丝抖动。这种方法较简便,而且不需调整加工电参数。
(2)加工厚工件时的断丝。厚工件一般指大于100mm的工件。切割厚工件时的断丝可能发生在刚进给一产生火花时或工件切割过程中以及工件切完时。断丝的主要原因是:
①切割起始的断丝。从工件外进给切割刚产生火花就断丝。这是因初始切割时,钼丝在工件之外,上下导丝轮开距大,由于钼丝没有阻尼而抖动,使钼丝和工件之间的间隙处于不佳状态,或过量的乳化液,造成绝缘电阻降低,灭弧性能不好,使放电间隙中包含了电弧放电而造成铜丝烧伤。在电火花加工中,电弧放电是造成负极腐蚀损坏的主要因素,再加上间隙不佳,易形成电弧放电。而只要电弧集中于某一段,就会引起断丝。并且,短路电流越大,电弧对钼丝的烧伤越严重,断丝的可能性就越大。
②切割过程中的断丝。当钼丝切人工件后,由于切缝窄,乳化液渗透困难,切缝中的电蚀物(碳黑与金属何不出来,使加工条件变坏,往往在切缝中二次。三次地放电加工,致使切缝变宽,和切割薄工件一样,间隙处于不佳状态,使脉冲形成电弧放电。如电弧放电集中于某一段,则很快会把钼丝烧断。
③切割快完时的断丝。在快切割完而尚差几毫米,甚至几十微米时断丝。产生这种断丝的原因除 上述原因外,还有工件的自重,工件材料的内应力导致的变形,造成夹丝拉断。解决的办法是,可自制简易的工装夹具,材料在加工前作必要的热处理。
(3)工件中夹有不导电物质引起的断丝。外观看似正常的材料在正常切割时,突然发生“短路”现象,不管怎样排除都不能奏效。这种情况多为在锻打或熔炼的材料中夹有杂质,这些杂质不具有良好的导电性,致使加工中不断短路,最终勒断钢丝。解决的办法是,可编制一段每进0.05~0.1mm便后退0.5~1mm的程序,在加工中反复使用,并加大冷却液流量,一般可冲刷掉杂质,恢复正常切割。
(4)线切割加工的工件多数都是在平磨以后,按正常的工艺,平磨后应退磁。若工件未退磁,线切割加工中产生的电腐蚀颗粒易吸附在割缝中,特别是工件较厚时,不退磁易造成切割进给不均匀,表面粗糙度值增大造成短路、断丝。
(5)线切割加工自动对中心时断丝。这是因为工艺孔壁有油污、毛刺或某些不导电的物质,当电极丝移动到孔壁时未火花放电,致使机床不能自动换向,工件将钼丝顶弯,最后勒断钢丝。因此加工前一定要将工艺孔清理干净。
1.3 与脉冲电源相关的断丝
(1)加工电流很大,火花放电异常,导致断丝。这种故障多数是脉冲电源的输出已变为直流输出所致。从脉冲电源的输出级向多谐振荡器逐级检查波形,更换损坏的元件,使输出为合乎要求的脉冲波形时才能投入使用。
(2)输出电流超过限值断丝。在加工过程中火花放电突然变为蓝色的弧光放电,电流超过限值,将钼丝烧断。用示波器测输人端和振荡部分都无波形输出。可判断故障出在振荡部分。检查发现有三极管的。立功极间内部开路,中极间内部击穿,更换此管,高频电源恢复正常。
另一种情况也是在加工过程中突然断丝,电流在限值以上。用示波器测量高频电源输出端,其波形幅值减小,并有负波,而脉冲宽度符合要求,测量推动级波形其频率、脉冲宽度及幅值均符合要求。判断故障在功放部分。检查功率管,测得其中一只管子的ce极间内部击穿,使末级电流直接加到钢丝与工件之间引起电弧烧断钼丝。换去该管,恢复正常。
(3)钼丝上出现烧伤点发生断丝。一旦钼丝上出现“疙瘩”状的烧伤点,极易发生断丝现象。一般认为,这是粘附在电极丝上的加工屑(阳极物质)所为,该粘附物起到了使放电集中在电极丝上的作用,此时若冷却散热条件差,就很可能使该处的温度升高,这样一来在连续的放电中就可能继续有其他加工屑粘附在该点附近,如此造成一种恶性循环,最后导致该处发生烧伤现象。
至于为何加工屑会粘附到电极丝上的问题,其主要原因与脉冲参数和放电间隙的冷却状况有关。解决的办法是,可提高脉冲电源的空载电压幅值,或采用双脉冲法门类似于通常所说的分组脉冲),这样可减少加工屑粘附到电极丝上的可能性;加大冷却液流量,改善冷却条件。
(4)钼丝上出现烧蚀点发生断丝。在钢丝额中,每隔一段(约10mm左右)即有一个烧蚀点。轻微的像一个霉点,严重的可明显看到钼丝的烧蚀点。这是由于电极丝与工件间拉弧所造成的,因某种原因使工件上A点与钼丝上B点拉弧,电极丝在运动,A、B二点间的拉弧越拉越长,A点又与最接近的B’点开始拉弧,如此周而复始,即形成有规律间隔的蚀点,使电极丝的强度大大下降。产生这种现象的原因主要是进给系统末级输出不平衡,调整进给系统,这种现象即可消除。
1.4 与走丝装置及工作液相关的断丝
(1)与走丝装置相关的断丝,其根本原因还是该装置精度变差,尤其是异轮的磨损,会增加钼丝的抖动,破坏火花放电的正常间隙,易造成大电流集中放电,从而增加断丝的机会。可从3个方面去检查导轮机构的精度:
①导轮V形槽变宽。这会使电极丝在Y轴方向产生往复位移,表现在贮丝筒正反换向时出现不进给或跳进给的现象;
②导轮V形槽的底径不圆。这是由于支撑导轮的轴承损坏,加工时钼丝没有进人导轮的V形槽或有污物将导轮卡死,钼丝拉出深槽所致,当用手摇动贮丝筒时会发现电极丝在X轴方向前后移位;
③导电轴与导电轮接触不好引起断丝。加工中发现电流表指针左右摆动大,进给速度快慢不均匀,有时电流表指针退回到零,控制台进给速度很快,因没有放电,最后将钼丝拉断。这时要更换新的导电轮和导电轴。
(2)对要求切割速度高或大厚度工件,其工作液的配比可适当淡一些约5%~8%的浓度,这样加工较稳定,不易断丝。
(3)工作液脏污,时间用长后综合性能变差是引起断丝的重要原因。实践中,可这样来衡量工作液是否变差:当加工电流为2A左右,其切割速度为40mm2/min左右,每天工作8 h,使用两天后效果最好,继续使用8~10天则易断丝,须更换新的工作液。
(4)有研究认为,用高纯水配置的工作液加工时工作稳定,较少断丝。其原因是估计高纯水在离子交换提纯的过程中去除了某些有害于电蚀加工的离子,如钙离子、镁离子等,致使在加工过程中,虽有电蚀产物的介人,使工作液中混入了各种离子,但由于清除了有害离子而得以使加工稳定。
1.5 与材料相关的断丝
(1)一般认为未经过锻打、淬火、回火处理的金属易断丝。这是因钢材中碳化物分布不均匀,引起电加工性能不稳定造成电弧放电而断丝。钢材中所含碳化物颗粒大,并且聚集成团,而分布又不均匀。这样的材料加工中易开裂、变形夹牢钢丝,造成断丝。尤其是淬火件,淬火后,在无碳合金中约存在500~800MP。的内应力,在高碳钢中则可有达1600MPa的内应力,若经过磨削加工,还可引起70~80MP。的内应力,而放电加工会在其加工表面上形成白色的放电加工变质层,并产生约 800MPa的拉应力。淬火应力、磨削应力、放电加工应力交互迭加引起应力集中是导致淬火件在线切割加工中开裂而导致断丝的直接原因。因此,为减少因材料引起的断丝,应选择锻造性能好、淬透性好。热处理变形小的材料,促使钢材中所含碳化物分布均匀,从而使加工稳定性增强。如以线切割加工为主要工艺的冷冲模具;尽量选用 CrWMn、 Cr12Mo、GCr15等合金工具钢,并要正确选择热加工方法和严格执行热处理规范。
1.6 其他
(1)在拆丝时,往往用剪刀将贮丝筒上的旧丝剪断,形成很多短头,若不注意清理会混到电器部位中或夹在走丝装置中,引起短路,造成断丝。
(2)加工完成后,应首先关掉加工电源,之后关掉工作液,让丝运转一段时间后再停机。若先关工作液,会造成空气中放电,形成烧丝;若先关走丝的话,因丝速太慢甚至停止运行,丝冷却不良,间歇中缺少工作液,也会造成烧丝。
(3)某些时候需要手动切割时(指手摇十字滑板),应眼观电流表,不得超过正常切割时的变频速度,否则极易断丝。
(4)实践中,有因污垢引起的断丝现象,这种现象往往在加工完工件后出现。检查时用万用表电阻挡测量出钢丝与机床外壳之间有30k?左右的电阻,且调换笔有充放电现象。进一步检查发现钼丝挡块螺钉与线架之间,断丝检测块与固定在线架上的螺钉之间有很多液渣污垢。
拆下挡块和检测块后充放电现象消失,电阻值上升。这是因液渣污垢使钢丝与机床外壳之间形成一电阻电容,并联在功放管输出端上(因外壳与功放管射级等电位),而使输出波形底部变宽,直流成分增加。当工件快加工完时钼丝与工件间的间隙加大使采样电位升高进给速度加快,这就使钼丝在加工完时易断丝。清洗污垢后,机床恢复正常。
来自:求助得到的回答
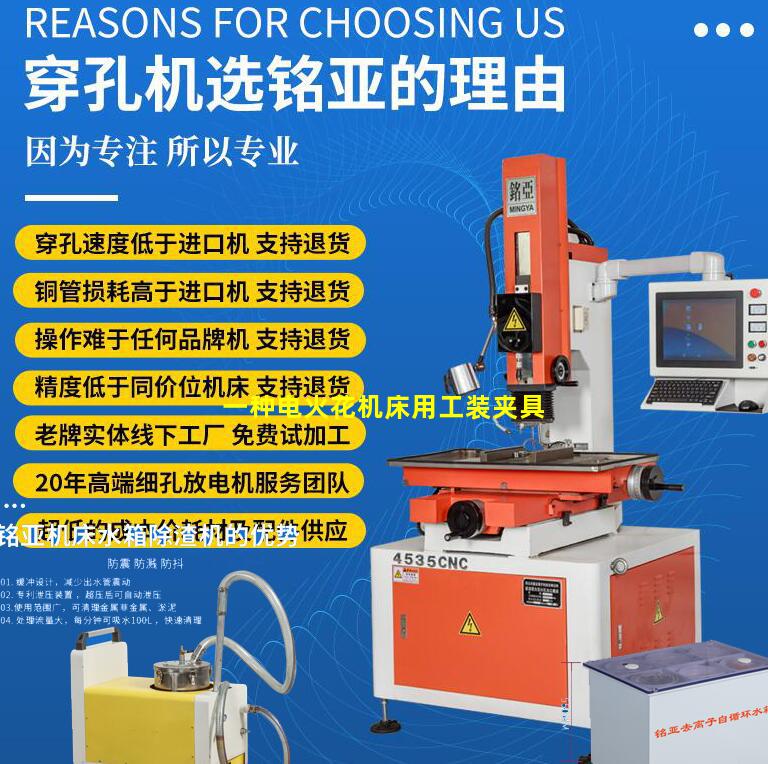
2、电火花加工工件装夹
是加工斜口吗?1先加工出你图纸上所需要的度数的斜块2小件的工件将工件放在斜块上装夹,现在工件打表分中碰单边就可以加工了3大件也是先加工一个小的斜块放在工件上方,工件下方找东西垫起来使钼丝与斜块垂直后打表分中碰单边这个方法对初学者来说难度还是比较大的,这只是原理建议先找个小点没用的东西试一下掌握后才去加工模仁
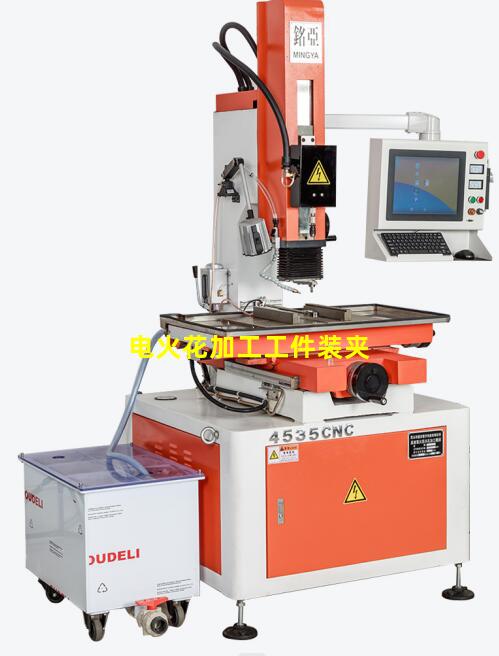
3、电火花加工用夹具价格
一般是以小时计费,小时计费一般是加工时间长的零件如加工镜面,小一点的就是谈价
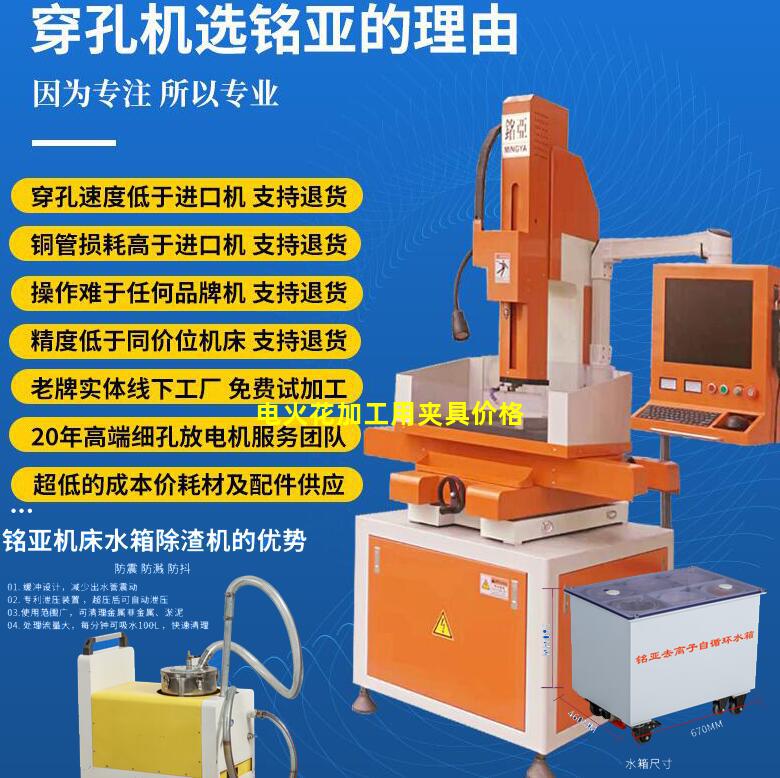
行业热门话题:
【电火花加工工件装夹】【电火花加工用夹具价格】【电火花线切割加工常用的夹具主要有】【数控电火花成型机床的工具是】【电火花加工常用机床】【常见电火花加工机床主要包括】【电火花机床的结构】【电火花加工机床有哪些附件】【在电火花线切割机床上安装工件时】【电火花加工常用的机床是电火花】
即将到来的节日:9月中秋节放假3天!再忙也要对自己好点哦!
江阴城东街道一种电火花机床用工装夹具-电火花线切割加工常用的夹具主要有完!